Case Study
Smiley Monroe’s ZIP CLIP® Belts are transforming downtime in the recycling industry
Updated on: 13 June 2025
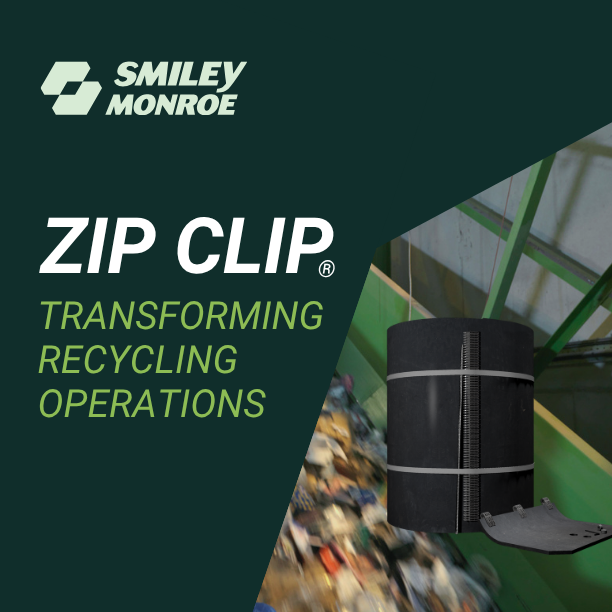
Discover how Smiley Monroe’s ZIP CLIP® replacement conveyor belt turned a downtime disaster into a quick recovery, helping transform our customer’s operations & save them thousands in lost revenue.
We manufacture products designed to maximise uptime, and when a large recycling plant recently suffered multiple conveyor breakdowns, it was Smiley Monroe’s ZIP CLIP® replacement conveyor belt that turned a downtime disaster into a short-term breakdown.
The customer operates a fully integrated waste management and recycling company, processing waste from a number of sectors and currently treating over 350,000 mt of waste each year diverting up to 250,000 mt of waste from landfill into recycling plants or waste-derived fuels.
Downtime planned or unplanned on any plant can cost up to £1000 per hour in lost revenue as well as a hefty vulcanising bill and lost time waiting for a crew to arrive. Material building up and waiting to be processed can also quickly cause a logistical problem if plants are not up and running. The process of vulcanising endless belts on site also led to a number of health and safety implications, with service teams operating at height and lift equipment having to be hired at additional costs.


Recognising the customers’ challenges, our product support team recommended the customer trial Smiley Monroe ZIP CLIP® mechanically fastened conveyor belts as an alternative to the vulcanised belts. The customer adopted the trial into one production facility and found that their planned maintenance downtime was slashed – saving thousands in lost revenue and vulcanising costs. The ZIP CLIP® belts could be fitted in just one hour, without the need for hiring safety equipment or a specialist team. So successful was the trial, that the company has now rolled out ZIP CLIP® replacement belts as standard across their entire operations.
Smiley Monroe’s short lead times and premium dispatch service on ZIP CLIP® belts mean that even in the case of a conveyor breakdown, the customer can receive a belt as soon as the next day depending on location. Switching to the world’s fastest replacement conveyor belt has transformed the customer’s maintenance costs and significantly reduced the impact of downtime on their business.
To find out more about ZIP CLIP® the world’s Fastest Replacement Conveyor Belt – Click Here